Driving Digital Transformation
Forecasts of social disintegration and wide-spread unemployment caused by Industrial IoT are a melodramatic overreaction stemming from the fear of change. To the horseshoe smithy, the car also posed an existential threat – but does that mean we should return to the dark ages? Judith Ellis explores the attitudes to digital transformation, the challenges from smaller companies, and the steps needed to make it a success.
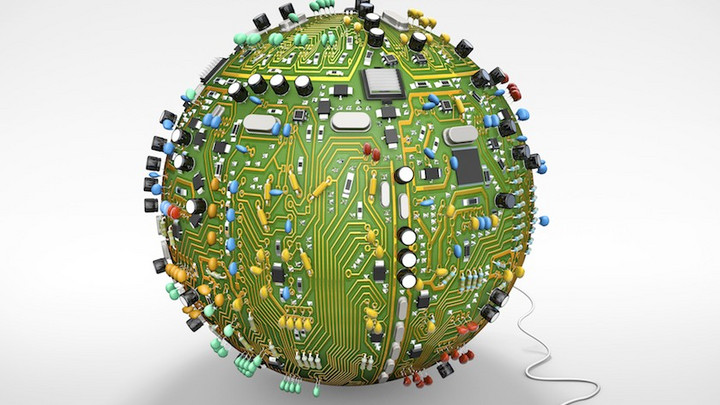
© francisbonami | iStockphoto
It is perhaps understandable that the driverless car, more than most other innovative IoT concepts, has experienced the sharp end of the media tongue: the pariah that is going to take away the jobs from so many hard-working taxi drivers – and by extension, truck drivers – in the future.
The driverless car represents human existential angst in a very vivid way. Driving a car is an activity that most of us take for granted, something which offers us the freedom to escape from the rat race for a long weekend, something over which we personally have power and control. Autonomous driving takes that control away from us, and this makes us feel insecure – what if there is a computer malfunction? What if it gets hacked? What’s more, the concept erodes a physical skill that forms a part of our identities as modern humans – I drive, therefore I am.
And as such, the driverless car is often taken as a symbol for the entire process of the digitalization of society and industry – seen through angst-colored glasses, it evokes the loss of liberty, loss of control and security, and loss of employment.
Digital transformation as empowerment
But seen from another angle, the driverless car is indicative of the empowerment that digital transformation offers. It frees up resources – that driver is capable of concentrating on things other than the road, perhaps reading the newspaper, writing a report, or talking to family. It offers far greater accuracy – human error is responsible for the vast majority of traffic accidents, not mechanical or computer errors. And it enables economic growth in new and innovative forms, and will provide new and different work places for the future, even if, as with the blacksmith at the beginning of the automobile age, the profession of taxi and truck driver vanishes into the annals of history.
As computer scientist and IoT expert Dr. Bettina Horster from VIVAI Software points out, the western world is facing stark demographic change. One of the ways of combatting this will be to automate jobs that do not require human intervention. Although, according to Marco Comastri from CA Technologies, “the McKinsey Global Institute argues that less than 5 percent of occupations are likely to become fully automated. Instead, many will be partially automated.”
And no, it will not erode our skills base, any more than the computer eroded our capacity to handwrite – instead, we now have smart pens and computers that can interpret our scribbles. However, developing our education systems to support digital education will be another fundamental requirement for the digital age. There will not be fewer jobs at the other end of the transformation process – but there may well be fewer menial ones.
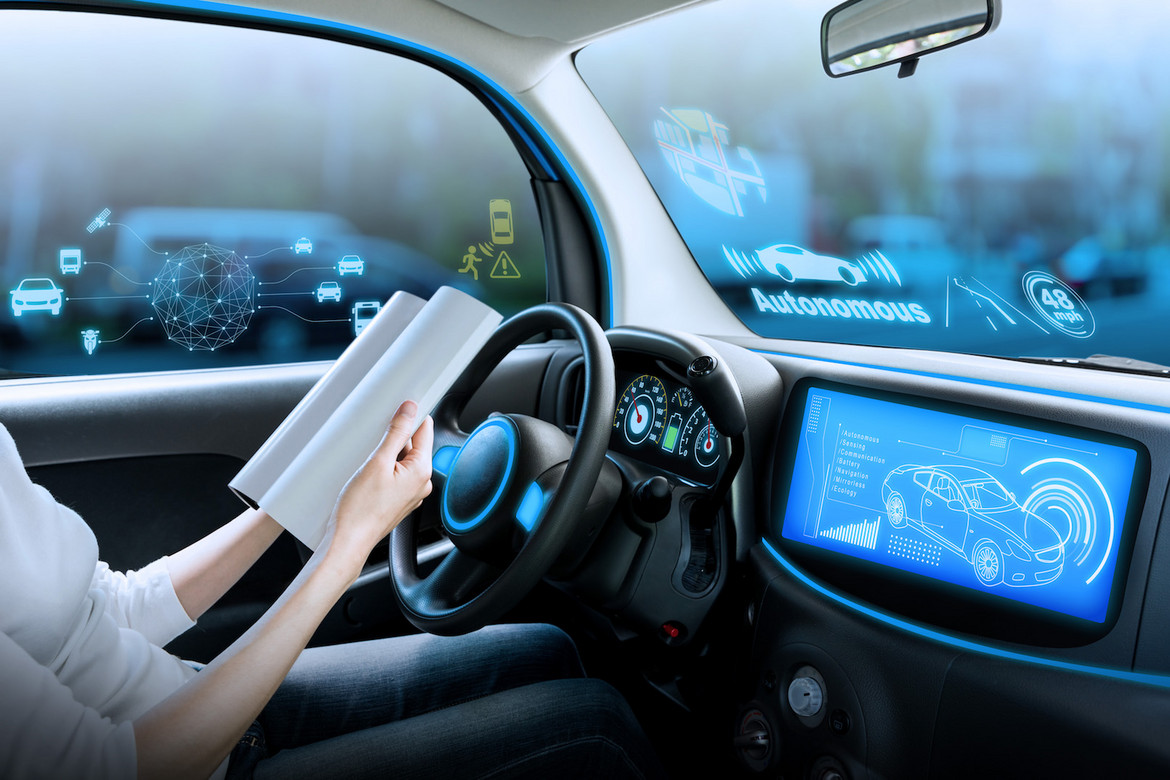
© chombosan | iStockphoto
Making industrial IoT safe
The existential angst, however, needs to be combatted on more sides than just the consumer end. There are risks with any transformation processes – and learning from the mistakes of others can help companies to avoid those pitfalls themselves. One area where this is the case is cyber security. Security expert Wolfgang Strasser from @-yet offers the story of the impact of a computer virus on one manufacturer with 24/7 production and just-in-time delivery and an insecure systems – business continuity plans are not only needed for natural disasters any more. Recent ransomware attacks have shown us that.
Authentication goes hand in hand with other types of security, and it allows you to be certain that the data you are receiving from your cyber-physical systems has not been manipulated and is, in fact, coming from the device it says it’s coming from. If your business model is based on the accuracy of your data analysis, this is clearly essential. Klaus M. Brisch and Marco Müller-ter Jung from DWF Germany believe that “securing things in the Internet of Things poses new challenges for legal practice because of the great diversity and plurality of connected devices. When things communicate with each other, the traditional authentication methods such as passwords or tokens cannot be used. Connected devices have a need to provide trustworthy information not only among themselves, but also directly to users or infrastructure providers. Creating trust among different devices is a significant challenge, considering the large scale of devices.”
The potential of digitalizing the production process
But having secured and authenticated your systems, then we can focus on the potential.
Marco Comastri from CA Technologies tells us that “end-to-end automation is a key part of the transformation into a Modern Software Factory. With IT becoming increasingly complex, automation can reliably speed up processes and improve precision. It is the key to managing diverse and complex environments to drive business outcomes and free up employees’ time to focus on strategic work.” But it’s not necessary to completely re-build legacy production facilities to start taking advantage of the benefits of industrial IoT. Predictive maintenance and digital monitoring of machinery and process, as Alexander Frese from ITENOS points out, “can also be performed in old facilities through retroactive installation of modern sensors.”
Looking outside the actual plant, “there are certain types of problems that are just not solvable by physical methods”, according to Andy Long from Hydro66 – advocating the value of digitalizing the design, testing and simulation of products using High-Performance Computing. He continues, “when you look at some of the more interesting or more kind of out-there applications I've read about (…), you can rapidly decrease the time to market for products, but also make massive savings in the development.”
And production has taken a completely different turn in the last few years, with the advent of manufacturing-scale 3D printing technology. “Additive manufacturing is way past the point of only being used for the construction of prototypes. The concept is also applied when manufacturing end products. In the context of 3D printing, this is accompanied by modified production processes, the usage of new raw materials, altered delivery, and performance relationships as well as innovative business concepts, leading to multiple legal questions,” according to Brisch and Müller-ter Jung. “For companies involved, it is of particular importance to detect the complexity of those legal questions and their interrelations early on in order to exploit the full economic potential of their business by including solutions to those issues in the relevant business model.”
Challenges for industial IoT
So there is plenty of potential for digital production in all its forms. There are, however, a few other challenges to be managed.
Dealing with the massive amounts of data generated by industrial IoT is a fundamental issue. “With data transmitted at one-second intervals, enormous amounts of data will thus be generated that must be transmitted via communication networks,” according to Alexander Frese from ITENOS. “Many companies use different provider contracts to cope with the requirements for communications and content, leading to a highly complex meshwork of connections and interconnects at numerous providers. And this meshwork is expensive and not by any means fail-safe.” He goes on to say that “it is important to reduce the complexity of connectivity. This can be achieved by engaging only one single provider. It not only reduces the connection costs, but also improves the business overview of the cost structure and it facilitates the different digital services.”
Location also becomes a question companies need to deal with. Additive manufacturing means that production can take place on location, rather than being transported there from centralized plants, perhaps overseas. Equally, as Andy Long points out, “the cost of bandwidth has been falling exponentially, and at the same time the cost of power has been going up. And so, instead of taking power to these centers of information and population, we're now seeing the data being taken to centers of power.”
Developing trust in digital production
But in the end, perhaps the biggest hurdle to overcome is trust itself. As Dr. Horster tells us, “everybody tells you or tells the owner of the company: oh, you have to protect yourself, you have to be safe and you shouldn’t share your intellectual property - you have to keep everything to yourself. And now, when you start to work with the industrial Internet, it is also about connecting with the supplier and with your customers. It's about telling them about your interfaces.” Suddenly, companies are being expected to open up their systems to their business partners.
But just as suddenly, society is being asked to trust that the self-driving car is safe. That the fourth industrial revolution will make our lives better. That our children will have jobs in twenty or forty years’ time. Let’s look back again to the advent of the automobile. Yes, some jobs that had been essential until then became a thing of the past. Yes, industries and logistics were transformed. But the horse and coach had had its day.